DFG und Fraunhofer-Gesellschaft fördern Transferprojekt im Maschinenbau
- Forschung
- Top-Meldungen
- Medieninformationen
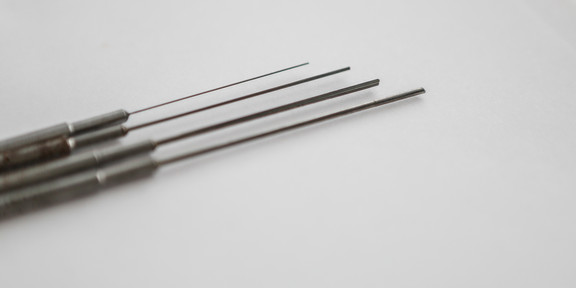
Prof. Dirk Biermann und Prof. Markus Stommel von der Fakultät Maschinenbau der TU Dortmund forschen gemeinsam mit dem Fraunhofer-Institut für Zerstörungsfreie Prüfverfahren und Partnern aus der Praxis zur Verbesserung von BTA-Tiefbohr-Verfahren. Die Deutsche Forschungsgemeinschaft (DFG) und die Fraunhofer-Gesellschaft fördern das Projekt, das den Transfer von wissenschaftlichen Erkenntnissen in die Anwendung ermöglicht, für drei Jahre.
Die DFG und die Fraunhofer-Gesellschaft fördern zum ersten Mal gemeinsam sieben Projekte zum Transfer von Erkenntnissen aus DFG-geförderten Vorhaben in die Wirtschaft. Die Fördersumme für die ausgewählten Kooperationsprojekte beträgt insgesamt sechs Millionen Euro. In den neuen Projekten arbeiten Hochschulen, Fraunhofer-Institute und Unternehmen trilateral zusammen. Für das Projekt „Leichte und schwingungsdämpfende hybride FVK-Metall-Rohre mit strukturintegrierter Sensorik für BTA-Tiefbohrprozesse“ kooperiert die Fakultät Maschinenbau der TU Dortmund mit dem Fraunhofer-Institut für Zerstörungsfreie Prüfverfahren in Saarbrücken sowie den Anwendungspartnern BGTB GmbH aus Dortmund, CarboFibretec GmbH aus Friedrichshafen und Kaiser Maschinenbau und Zerspanungstechnik GmbH & Co. KG aus Toppenstedt. Projektleiter vonseiten der TU Dortmund sind Prof. Dirk Biermann, Leiter des Instituts für Spanende Fertigung (ISF), und Prof. Markus Stommel, der die Professur für Kunststofftechnologie innehat.
Ziel des Projekts ist es, das BTA-Tiefbohren zu optimieren. Hierbei handelt es sich um ein Verfahren, bei dem die Bohrtiefen um ein Vielfaches größer sind als die Durchmesser. Aufgrund der erforderlichen Werkzeuglänge kommt es dabei zu erhöhten Schwingungen des Werkzeugs und somit zu einem stärkeren Verschleiß der Schneiden und Führungsleisten sowie zu einer verminderten Bohrungsgüte. Durch den Einsatz von faserverstärkten Kunststoffen (FVK), die eine heterogene Struktur aufweisen, sollen die Schwingungen abgedämpft werden.
Enge Zusammenarbeit mit Unternehmen
Bei der Entwicklung eines hybriden FVK-Bohrrohrs können die beteiligten Projektpartner auf Erfahrungen aus der Grundlagenforschung zurückgreifen. Durch die enge Zusammenarbeit mit Unternehmen ist zudem – von der Konstruktion bis zur Einsatzvalidierung – die Expertise industrieller Partner sichergestellt. Diese können wiederum frühzeitig von Innovationen aus der Forschung profitieren.
Die sieben nun geförderten trilateralen Projekte wurden aus 20 eingereichten Projektanträgen aus den Ingenieur-, Natur- und Lebenswissenschaften ausgewählt.