3D Printer Combines Silicones and High-Performance Plastics
- Research
- Top News
- Press Releases
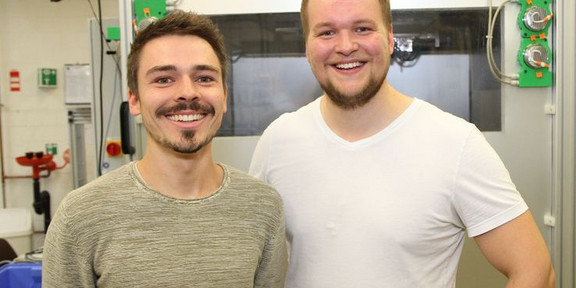
MedTech-Multiprint: With funding of around € 1.3 million, this project is one of the largest implemented so far at the Department of Machine Elements (ME) of the Department of Mechanical Engineering at TU Dortmund University. It is also the EXIST project with the most funding that the university has to date been able to secure. For the team led by Jasper Gruson, it represents an opportunity to start their own business with a high-tech project in a few years’ time.
The 3D multiprint printer is still standing “bare” in the workshop of the Department of Mechanical Engineering on North Campus: a cube with an edge length of about two meters. Wires, rows of screws, a sign warning about radiation: The model is a one-off and attests to a lot of manual work. “We mostly made it ourselves,” says Jasper Gruson. “Even the printer heads are our own developments.”
3D printer is unique worldwide
In the booming global market for 3D printers, this device is unique. The aim is for the printer to produce complex hybrid products. Specifically, it should make items out of different standard and high-performance thermoplastics, but also high-performance plastics and silicones, in a single, seamless production process. “One example of a concrete application is an artificial limb,” says Philipp Kemper. “If a person is reliant on such an aid, it has to be adapted individually.” This particularly applies for the point where the prosthesis is attached to the human limb: This interface must be made in such a way that it is skin-friendly and fits exactly. To achieve this, flexible, customized silicone pads are integrated into the prosthesis. This plastic-silicone combination is challenging because of the materials’ different properties.
The printer that Gruson and Kemper are developing can do it. At the same time, production is highly automated, resource-efficient and thus time-saving as well as inexpensive. With the production of components for individual aids such as artificial limbs, the first target market is medical supplies and the orthopedic sector. However, there are hardly any limits to possible applications – even as far as seats for Formula 1 drivers.
Gruson, Kemper and software developer Frithjof Pollmüller want to base the further development of this innovative 3D printing system on an existing laboratory prototype, that is, a special 3D printer built and put into operation in the framework of the project “FilChange – Flexible 3D Printing” within the ERDF program “START-UP – University Spin-offs in NRW”. The basis for the technology is a newly developed filament-processing module, for which TU Dortmund University has filed a European patent.
Workwise, the team of developers is proceeding in a number of steps – the project started on 1 March this year: First, they are optimizing the special 3D printer so that it can process high-performance plastics. At the same time, they are developing a new type of silicone-processing module. In the next step, they will create – for the first time ever in 3D printing – the possibility to process high-performance thermoplastics and silicones in one product. A new software solution will make it possible to connect the individual materials together in a time-efficient way and taking different load factors into account.
Support from the CET
With the EXIST program for the promotion of research transfer, the Federal Ministry for Economic Affairs and Energy funds outstanding, research-based start-up projects such as MedTech-Multiprint. The Center for Entrepreneurship & Transfer (CET) at TU Dortmund University is accompanying the team along its path to starting a business. “3D printing is a key technology of the future,” says Albrecht Ehlers, Chancellor of TU Dortmund University and member of the CET’s board. “I’m pleased that we can pave the way for this start-up from research to an independent business. This is a tremendous success on the part of our Center for Entrepreneurship & Transfer.”
Contact for further information: